Plastic extrusion for large-scale custom plastic parts
Plastic extrusion for large-scale custom plastic parts
Blog Article
A Comprehensive Overview to the Refine and Advantages of Plastic Extrusion
In the huge realm of production, plastic extrusion emerges as a extremely reliable and vital process. Altering raw plastic right into constant profiles, it provides to a variety of industries with its exceptional adaptability.
Recognizing the Fundamentals of Plastic Extrusion
While it may show up facility at very first look, the process of plastic extrusion is basically straightforward. The process begins with the feeding of plastic product, in the form of pellets, powders, or granules, right into a warmed barrel. The designed plastic is after that cooled down, strengthened, and cut right into desired sizes, completing the procedure.
The Technical Process of Plastic Extrusion Explained
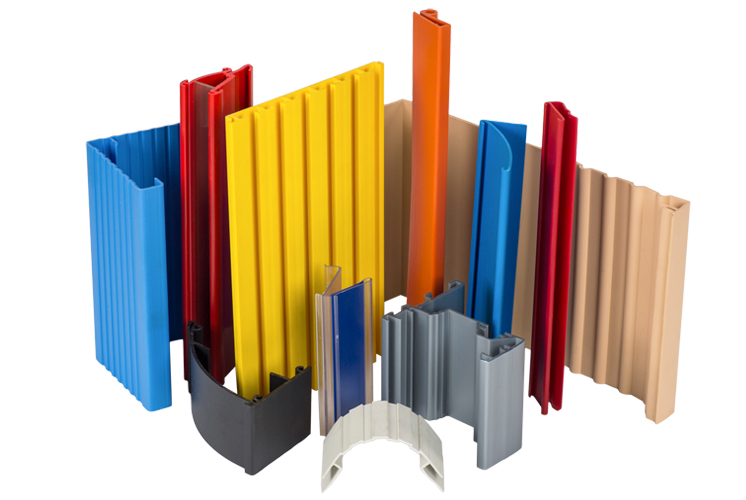
Kinds Of Plastic Suitable for Extrusion
The choice of the best kind of plastic is a vital element of the extrusion procedure. Different plastics provide distinct properties, making them more matched to particular applications. Polyethylene, for instance, is typically used because of its reduced cost and very easy formability. It provides superb resistance to chemicals and dampness, making it optimal for items like tubing and containers. Similarly, polypropylene is an additional preferred option as a result of its high melting factor and resistance to exhaustion. For even more robust applications, polystyrene and PVC (polyvinyl chloride) are commonly chosen for their stamina and toughness. Although these are usual choices, the choice inevitably depends upon the particular needs of the product being produced. So, recognizing these plastic types can significantly boost the extrusion procedure.
Contrasting Plastic Extrusion to Other Plastic Forming Approaches
Comprehending the kinds of plastic appropriate for extrusion paves the method for a broader conversation on just how plastic extrusion stacks up visit the website against other plastic forming approaches. Plastic extrusion is unparalleled when it comes to developing continuous accounts, such as seals, gaskets, and pipelines. It likewise allows for a consistent cross-section along the size of the item.
Trick Advantages of Plastic Extrusion in Manufacturing
In the world of manufacturing, plastic extrusion supplies several substantial benefits. One noteworthy benefit is the cost-effectiveness of the procedure, that makes it a financially enticing manufacturing method. Furthermore, this method gives superior product flexibility and enhanced production speed, consequently enhancing overall production effectiveness.
Cost-efficient Production Method
Plastic extrusion leaps to the forefront as a cost-effective production method in manufacturing. This procedure attracts attention for its capacity to generate high volumes of product quickly and efficiently, providing makers with significant savings. The main expense benefit is the capacity Your Domain Name to make use of more economical raw products. Extrusion makes use of polycarbonate materials, which are less costly contrasted to ceramics or metals. Even more, the extrusion procedure itself is fairly easy, decreasing labor expenses. Additionally, plastic extrusion requires much less power than standard manufacturing approaches, contributing to reduced operational prices. The procedure also lessens waste, as any kind of excess or faulty products can be reused and reused, supplying another layer of cost-effectiveness. Overall, the monetary advantages make plastic extrusion an extremely attractive option in the production market.

Superior Item Versatility
Past the cost-effectiveness of plastic extrusion, another considerable advantage in producing lies in its premium product versatility. This makes plastic extrusion an optimal remedy for markets that need personalized plastic components, such as vehicle, building and construction, and packaging. In significance, plastic extrusion's item flexibility promotes innovation while boosting operational efficiency.
Boosted Manufacturing Speed
A significant advantage of plastic extrusion lies in its boosted production rate. Few other manufacturing procedures can match the rate of plastic extrusion. In addition, the capacity to maintain constant high-speed manufacturing without compromising item quality establishes plastic extrusion apart from various other methods.
Real-world Applications and Influences of Plastic Extrusion
In the world of manufacturing, the strategy of plastic extrusion holds profound significance. The financial benefit of plastic extrusion, largely its high-volume and affordable output, has actually changed manufacturing. The market is persistently striving for developments in eco-friendly and recyclable products, suggesting a future where the advantages of plastic extrusion can be retained without endangering environmental sustainability.
Conclusion
Finally, plastic extrusion is a highly efficient and reliable technique of changing raw materials into varied items. It offers various advantages over other plastic forming methods, consisting of cost-effectiveness, high output, very little waste, and layout flexibility. Its effect is greatly felt in various markets such as building, automobile, and consumer products, making it a critical procedure in today's production landscape.
Digging much deeper into the technological procedure of plastic extrusion, it begins with the choice of the suitable plastic product. As soon as cooled down, the plastic is cut into the required sizes more or wound onto reels if the item is a plastic movie or sheet - plastic extrusion. Contrasting Plastic Extrusion to Various Other Plastic Forming Methods
Recognizing the kinds of plastic ideal for extrusion leads the method for a wider discussion on just how plastic extrusion stacks up against various other plastic creating techniques. Couple of other production procedures can match the rate of plastic extrusion.
Report this page